Add an outfeed table and tons of storage to your jobsite table saw with this amazing DIY table saw stand! Get the plans to build your own table saw workbench!
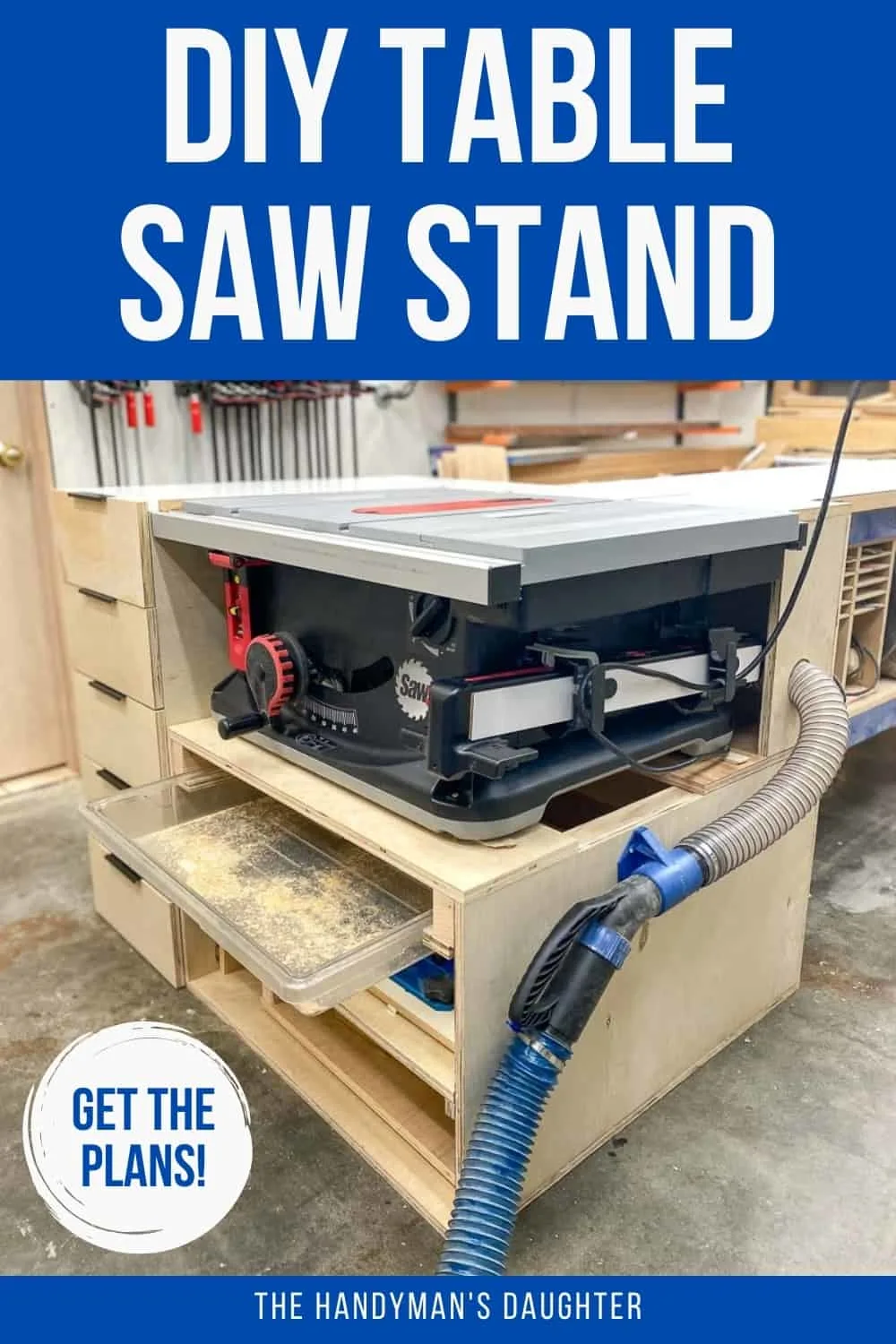
The table saw is the heart of the workshop, and I use mine for almost every project. But I only have a small jobsite table saw, which makes it hard to cut wider sheets of plywood or use some jigs and sleds properly.
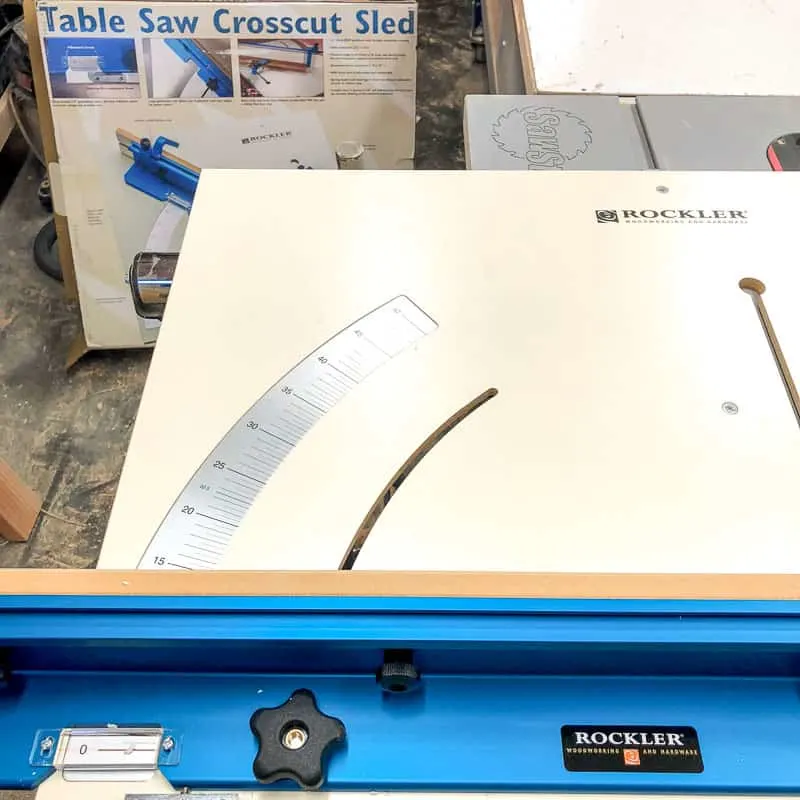
This post contains affiliate links for your convenience. Purchases made through these links may earn me a small commission at no additional cost to you. Please visit my disclosures page for more information.
As you can see above, this crosscut sled needs a lot more surface area to the left of the blade. Half the base falls off the edge, and the roller stand I was using isn't really ideal.
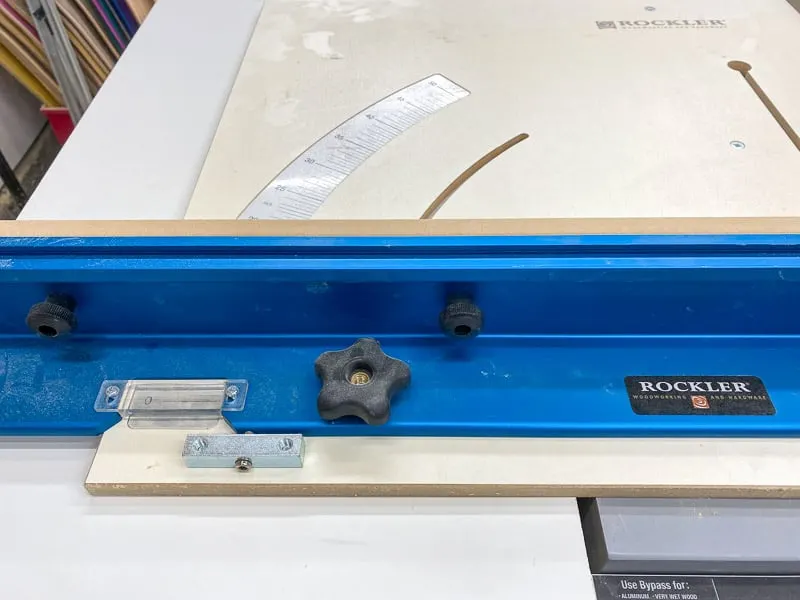
I designed this DIY table saw stand to fully support the crosscut sled, and made the top out of melamine so it can slide smoothly. Grooves in the outfeed table line up with the miter slots on the saw, and the stand is juuuust high enough to clear the top of my Kreg workbench behind it.
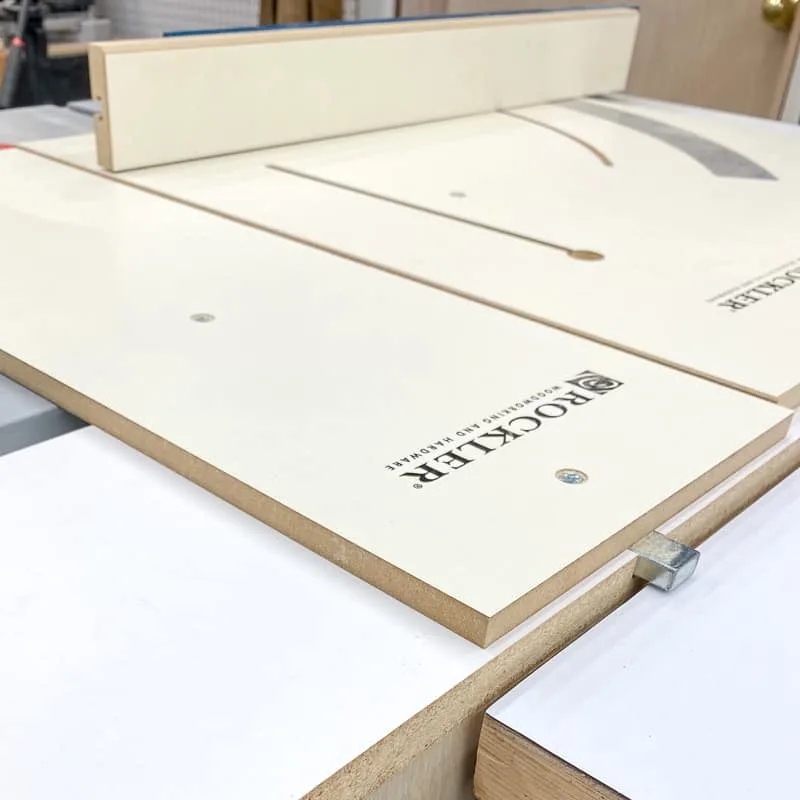
This small extension added a TON of storage space! I managed to squeeze five drawers and four shelves into the same footprint as the folding stand I had before. Now all the push sticks, featherboards and other table saw related gadgets are right where I need them!
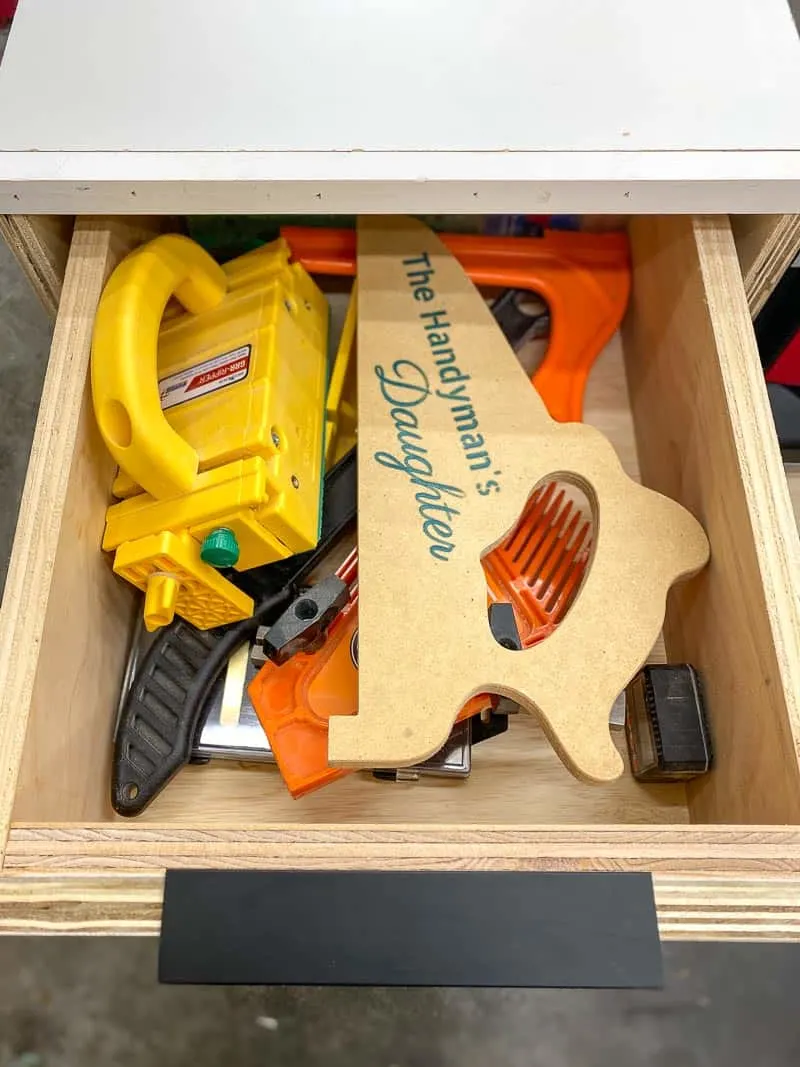
I've also improved the table saw dust collection! There's a dust port attached to the side, so I can hook up my wall mount dust collector hose easily. There's also a tray underneath to collect sawdust that falls through the bottom. I just vacuum it out every once in a while (or use the sawdust for other things), then slide it back into place!
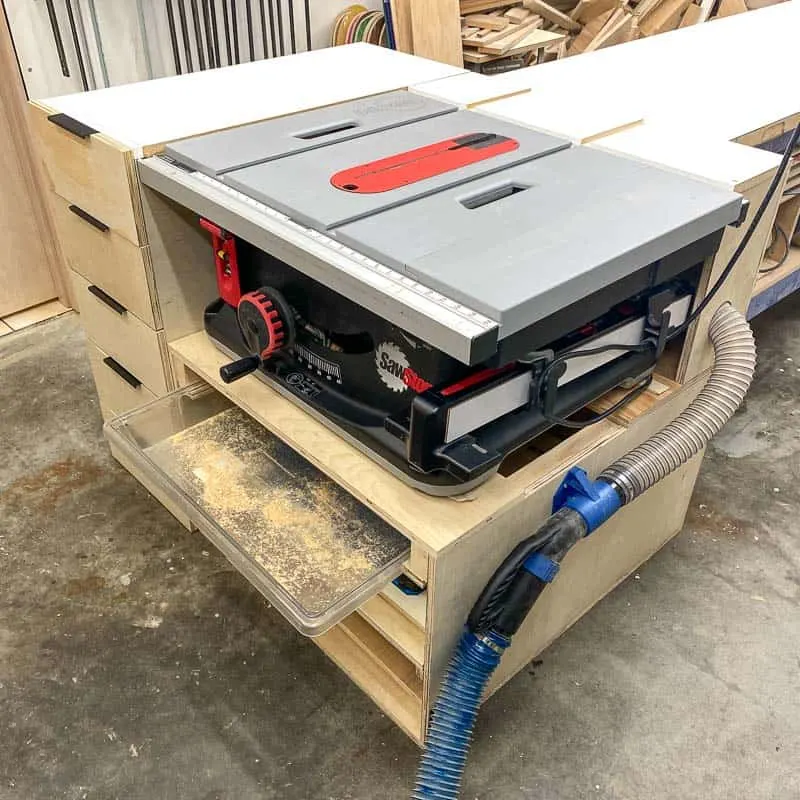
All my sleds and jigs are stored on shelves under the tray, instead of leaning up against the wall where they constantly fell over.
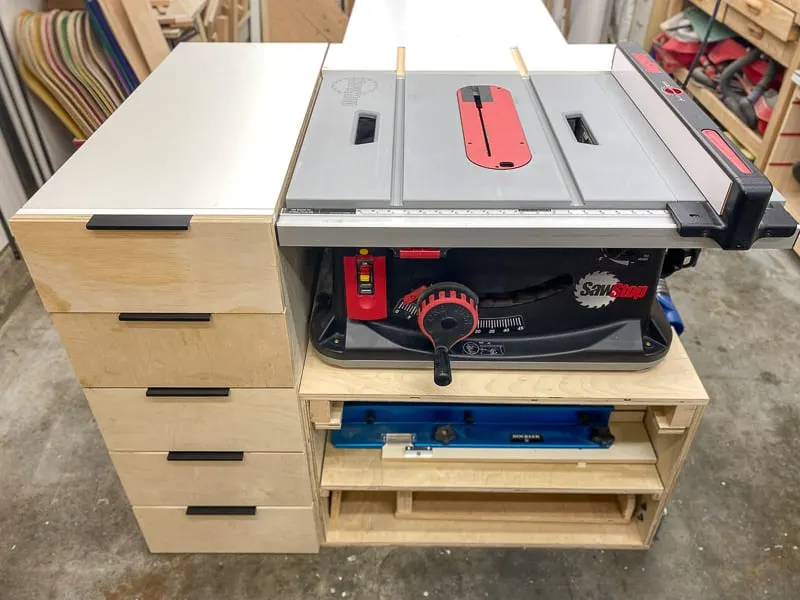
Ready to build your own? Check out the video below for an overview, then continue reading for the tutorial.
Materials needed for DIY table saw stand
- Two sheets of ¾” plywood
- Half sheet (48” x 48”) of ¾” melamine
- You can also use ¾” plywood for the top, but melamine slides better.
- Half sheet (48” x 48”) of ½” plywood for drawer boxes
- Half sheet (48” x 48”) of ¼” plywood for drawer bottoms
- Pocket hole jig
- 1 ¼” pocket hole screws
- 3” hole saw
- Dust collection hose to fit your table saw dust port (at least 16” long)
- Large tray for collecting sawdust (dimensions are sized for this one)
- Shelf pin jig and pins (or use pocket holes for fixed shelves)
- Five pairs of 16” drawer slides
- Five drawer pulls
How to make a table saw stand with storage
Download the plans
You can download the DIY table saw stand plans by clicking the button below! The printable plans include a detailed cut list and plywood cut diagram, step by step instructions with 3D models, and a handy checklist to keep you on track.
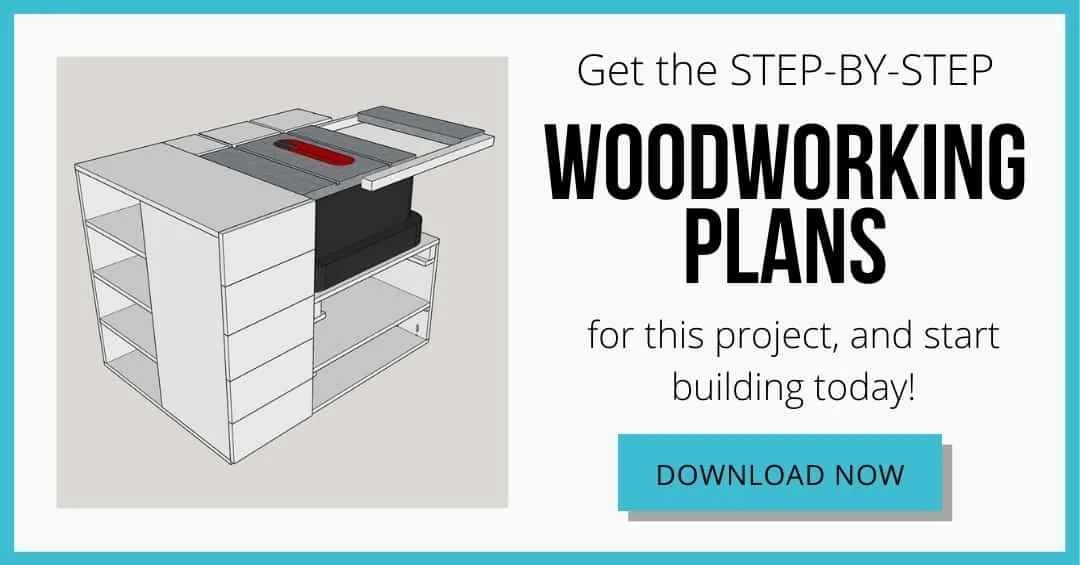
Measure your table saw
It's crucial that the top of the saw and the top of the outfeed table are exactly the same height. Otherwise, boards will catch on the higher edge and potentially kick back.
To measure the height accurately, place a board on top of the saw sticking out over the edge. Then measure the distance from the bottom of the board straight down to the floor. Then measure from the top of the stand (where the saw feet rest) to the floor, and subtract it from the overall height to get the exact height of the saw (ewwww, math!)
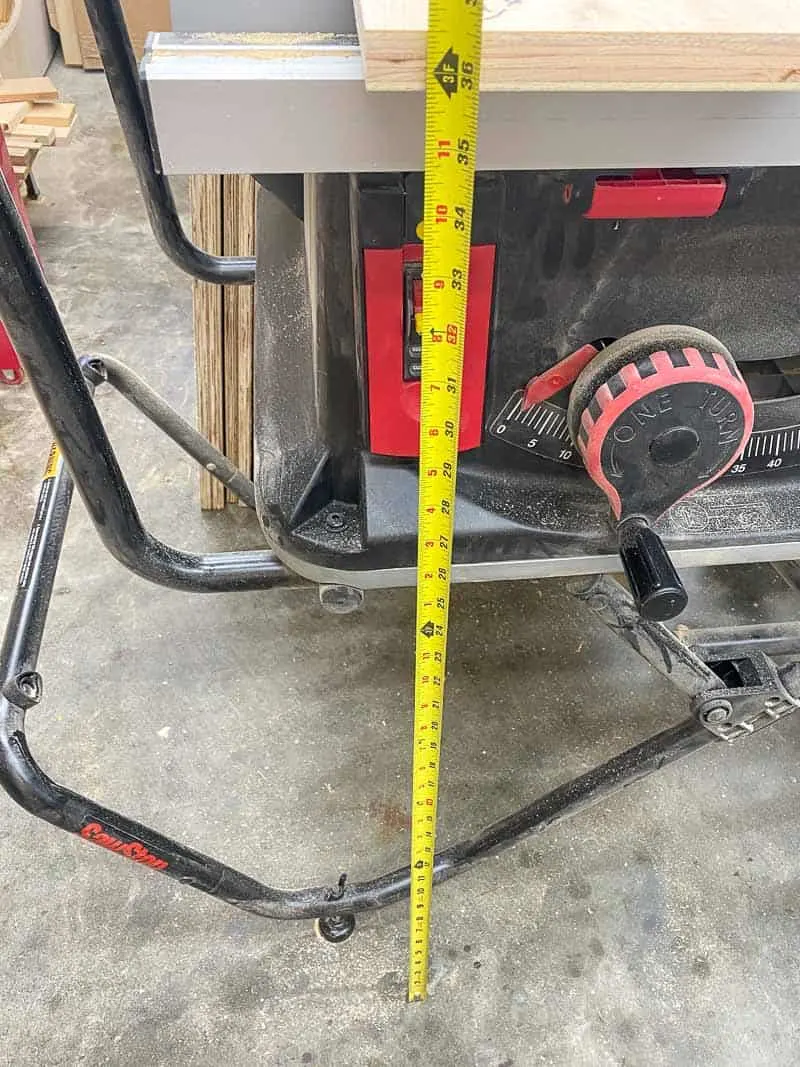
All the dimensions in the plans are for the SawStop Jobsite table saw (which is an amazing saw, by the way, and it won't chop off your fingers! 🙂 ) You'll need to adjust the size to fit your own saw according to your measurements.
Assemble the table saw base
Usually I would recommend using wood glue in all the joints, but not for this project. You won't know for sure if your measurements are correct until later on in the build, and you won't be able to take it apart to fix it if you use glue! Plus, I'll need to take the entire thing apart if we ever move, since my workshop is in the basement and it won't fit through the door.
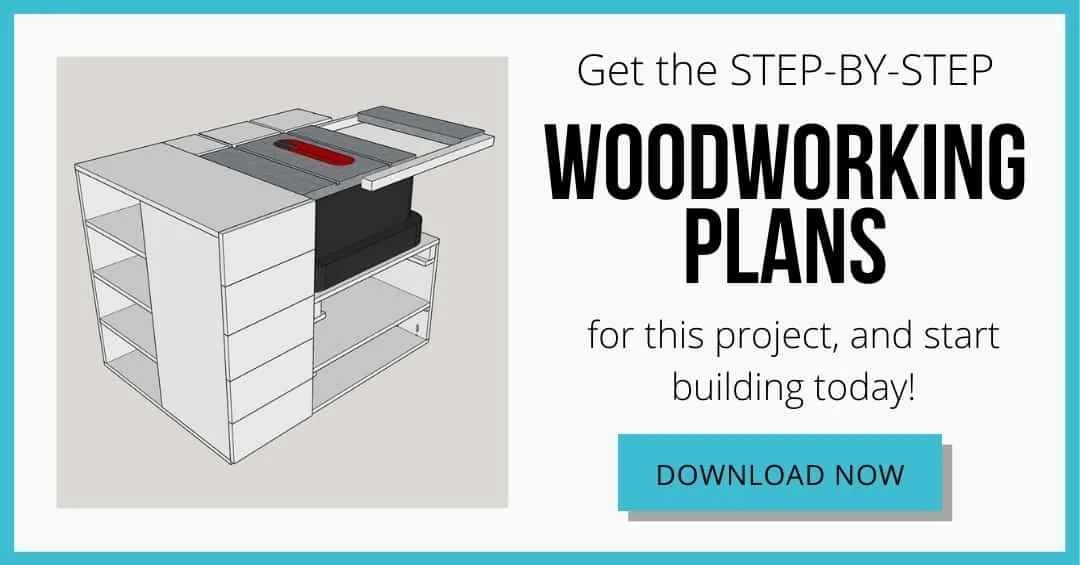
I used a track saw to cut the bigger pieces of plywood for the base, back and center panels, then drilled pocket holes as indicated in the plans to join everything together.
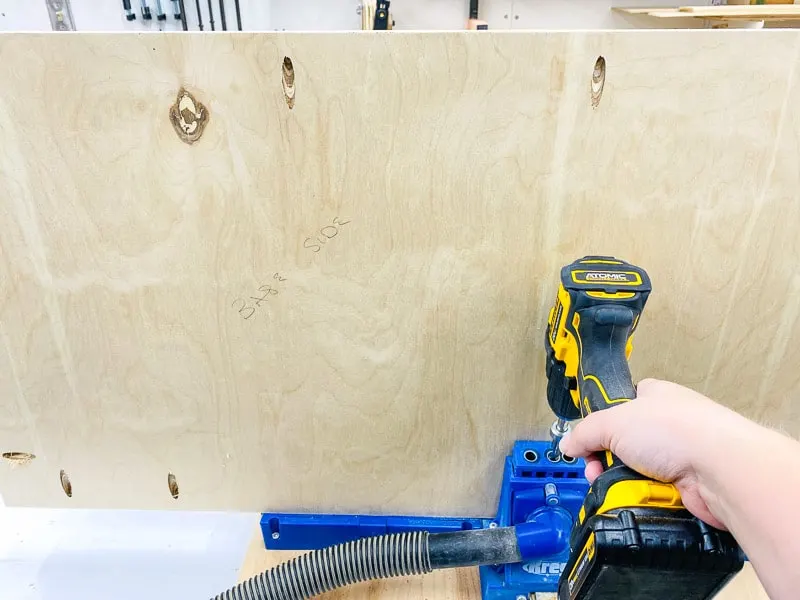
These bigger pieces can get a little unwieldy, especially when you're working alone. Assembly squares and a few clamps act as another set of hands to hold the parts at a perfect 90 degree angle while you screw everything into place!
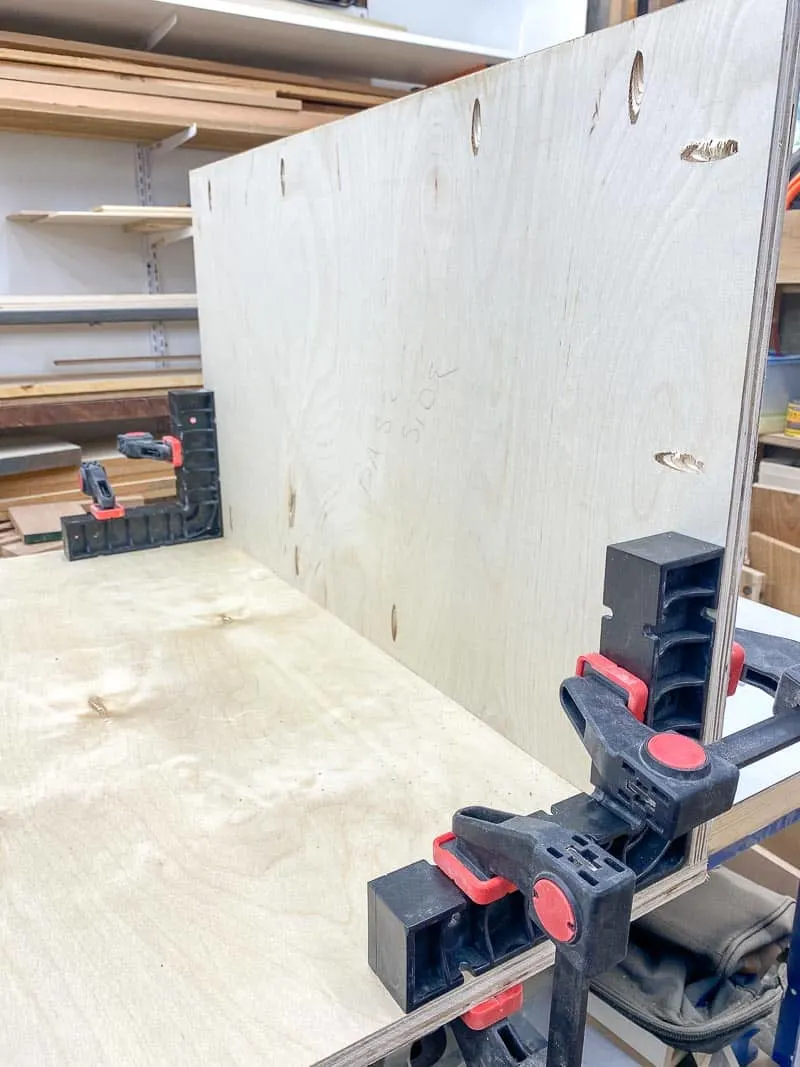
I used up a lot of scrap plywood for this project, which is why you'll see various types throughout the build. I tried to hide the ugly ones whenever possible, like this spot under the saw. The gap between the two boards will allow sawdust to fall through to the tray below.
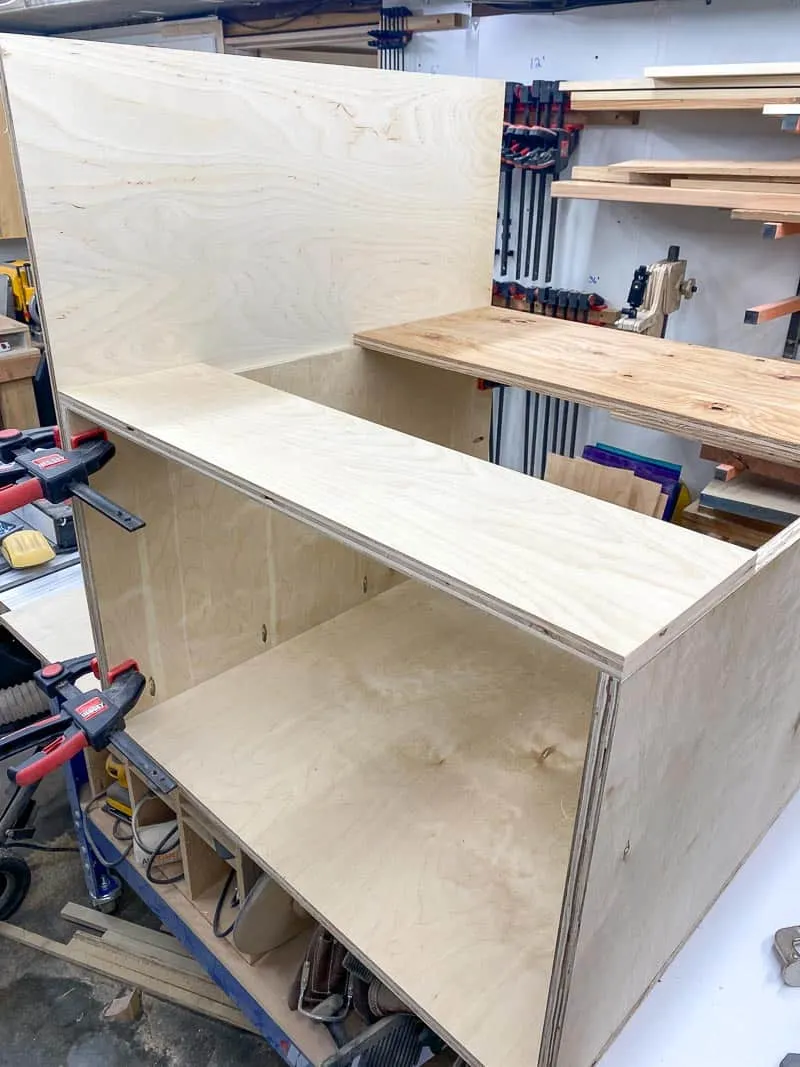
Once the base is assembled, you can place the saw on top and use it for the rest of the build!
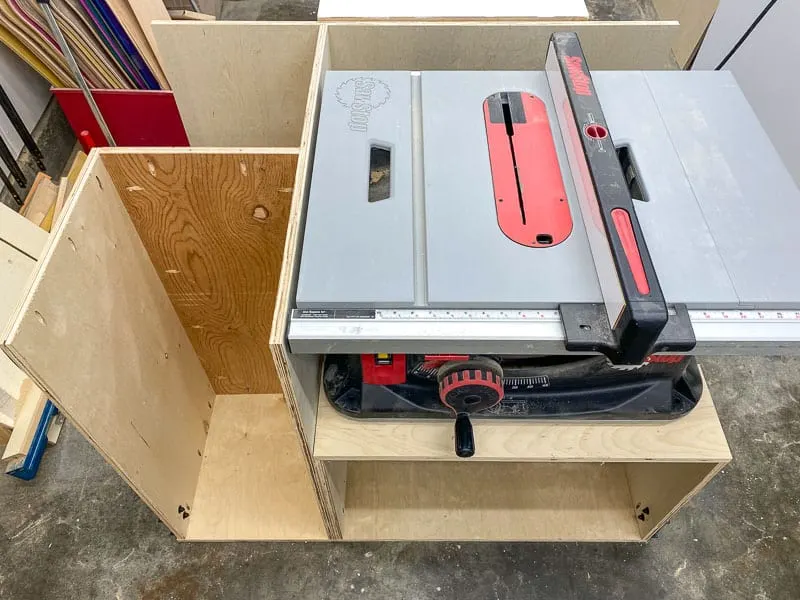
Install the top
The left side top and the back outfeed top are made from two separate pieces of melamine, to make it easier to cut the grooves. The scrap melamine I had for the left side was slightly too short, so I added a strip of preprimed trim to the end to make up the difference.
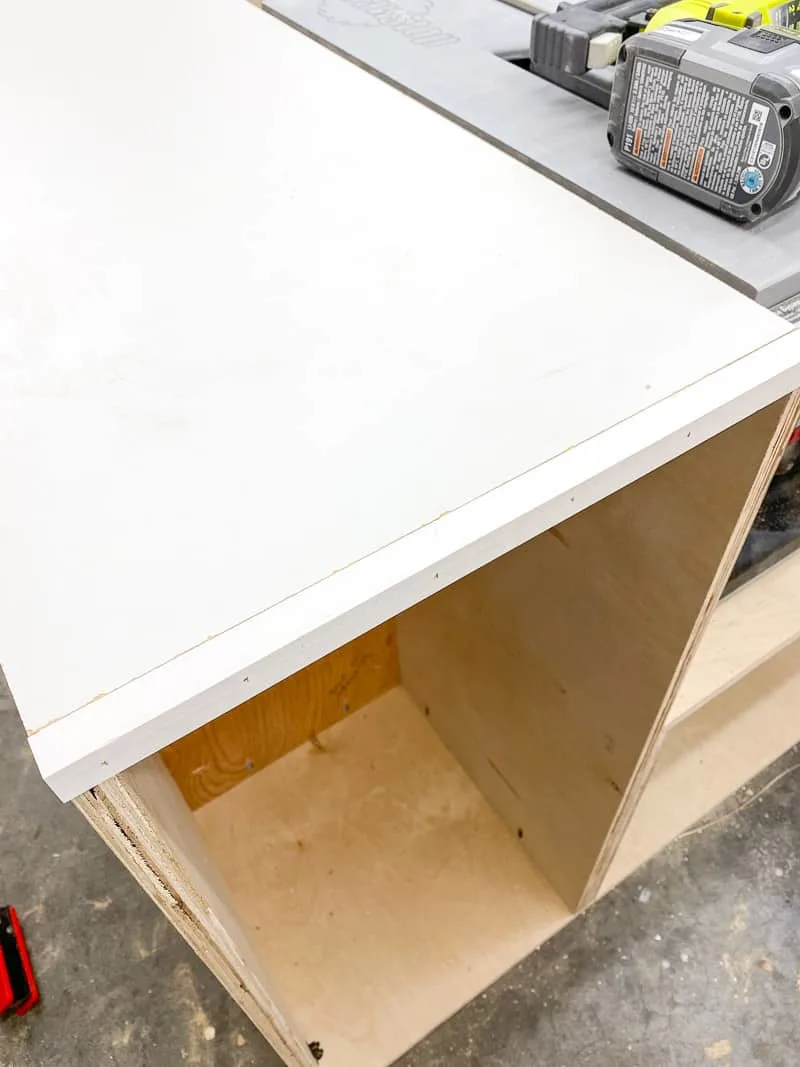
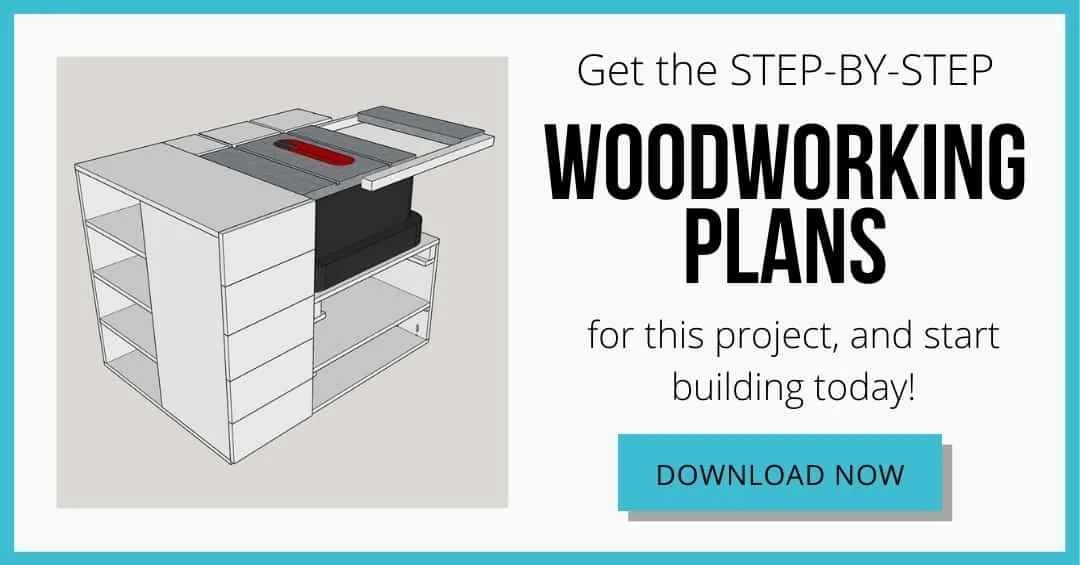
The back outfeed needed a bit more support, so I added end pieces to close up the sides, then drilled a 3" hole for the dust collection hose.
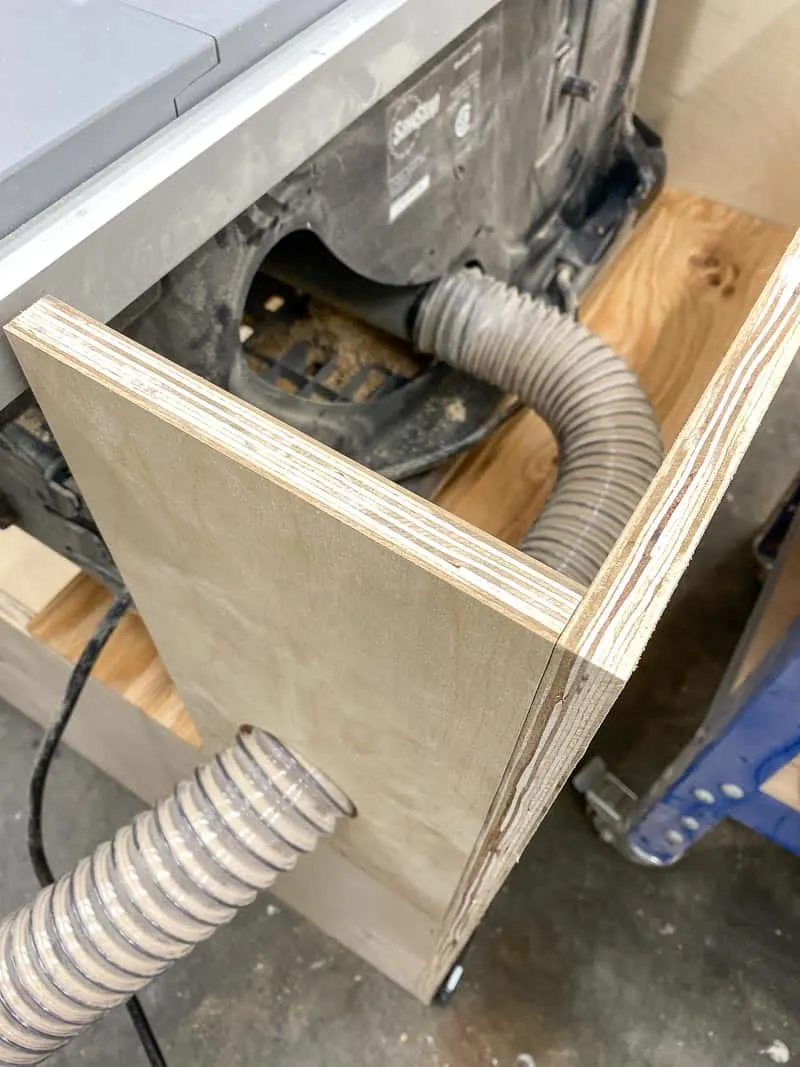
Mark the position of the miter slots onto the outfeed table piece. I used the runners of my crosscut sled to line them up perfectly, then cut the grooves on the table saw. You could also use a router for this step.
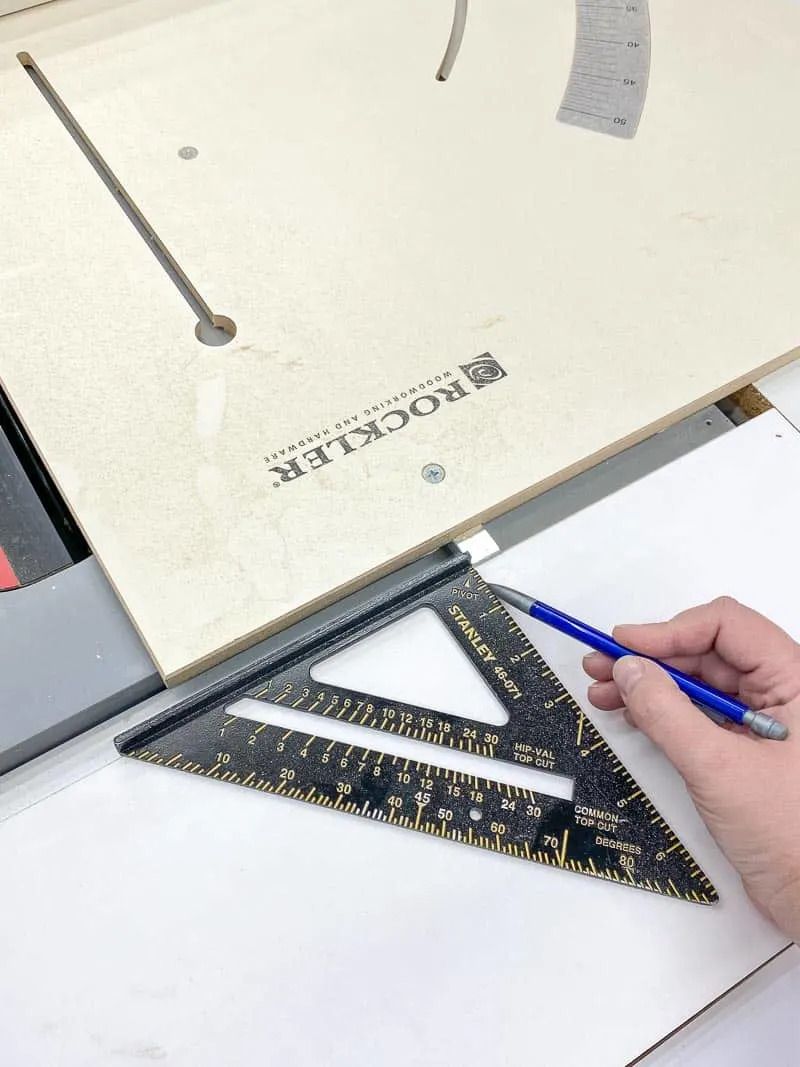
Make sure that the sled can move smoothly all the way through the groove. My workbench was already set to the right height to clear the runners. Then attach the top to the base with pocket holes (from the outside) and countersink screws, so it's easy to remove in case you need to access that space.
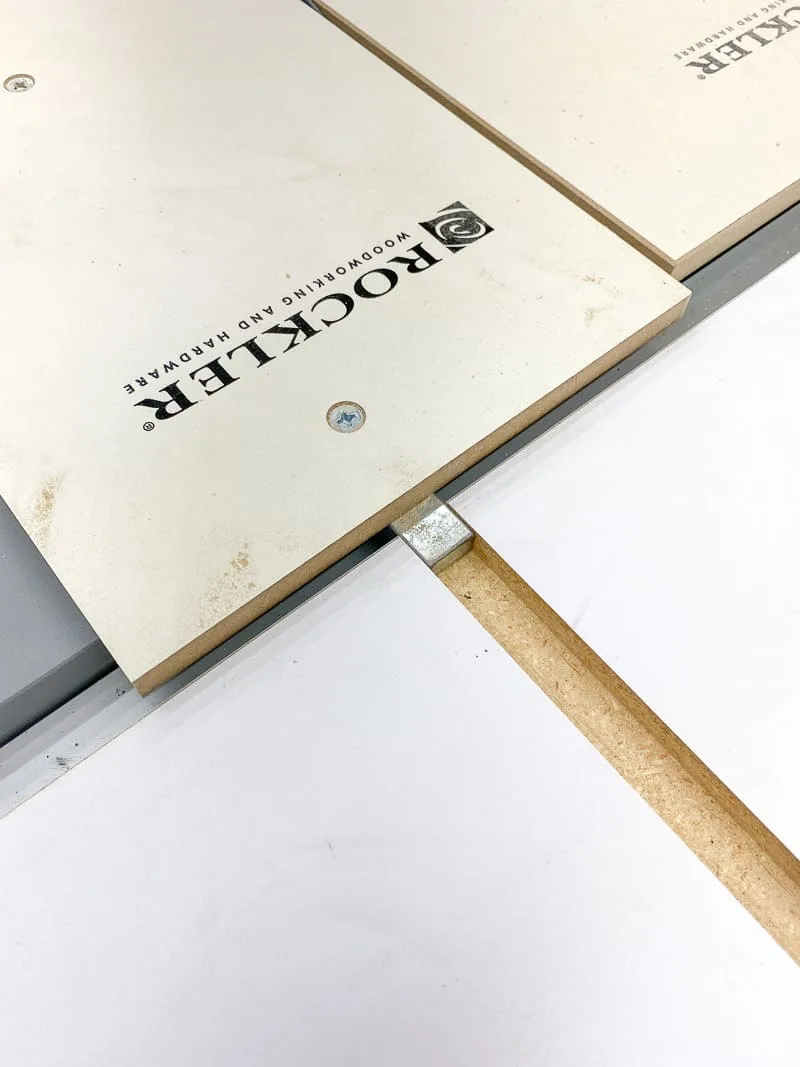
Add dust tray and shelf underneath the saw
The dust tray is just a plastic food storage container that you would normally find in a commercial kitchen. It's wide enough to span the entire underside of the table saw, but shallow so I can have enough space for two shelves underneath.
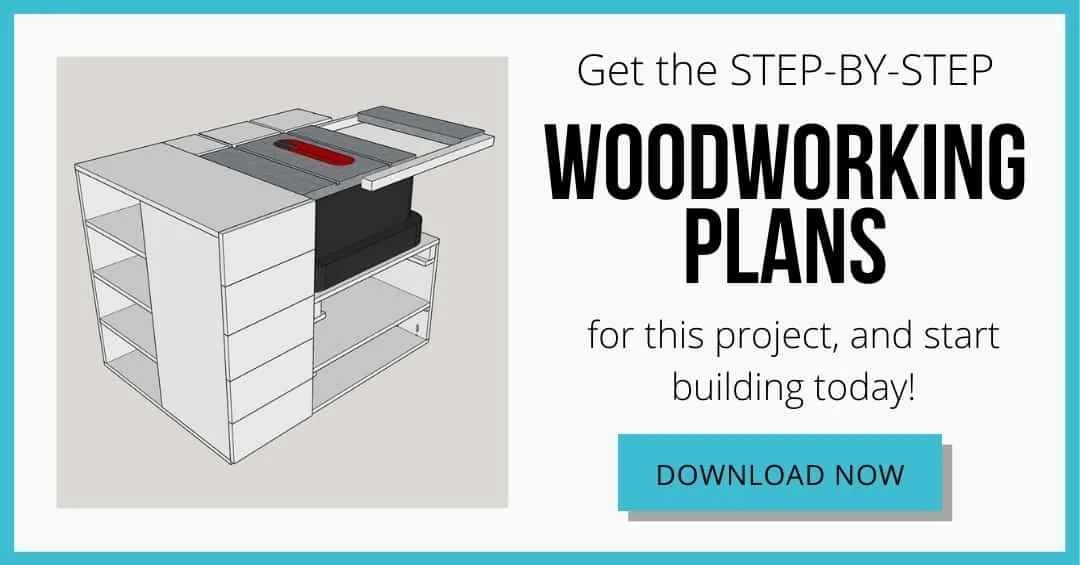
I created a bracket similar to the ones I used on my wall mount storage bins. It's just a 2x4 with a scrap of plywood attached to the bottom. Adjust the width of the plywood lip so that it holds the tray on both sides.

I didn't want the tray to slide all the way to the back, so I installed a stop that keeps it at the perfect spot for catching all that sawdust.
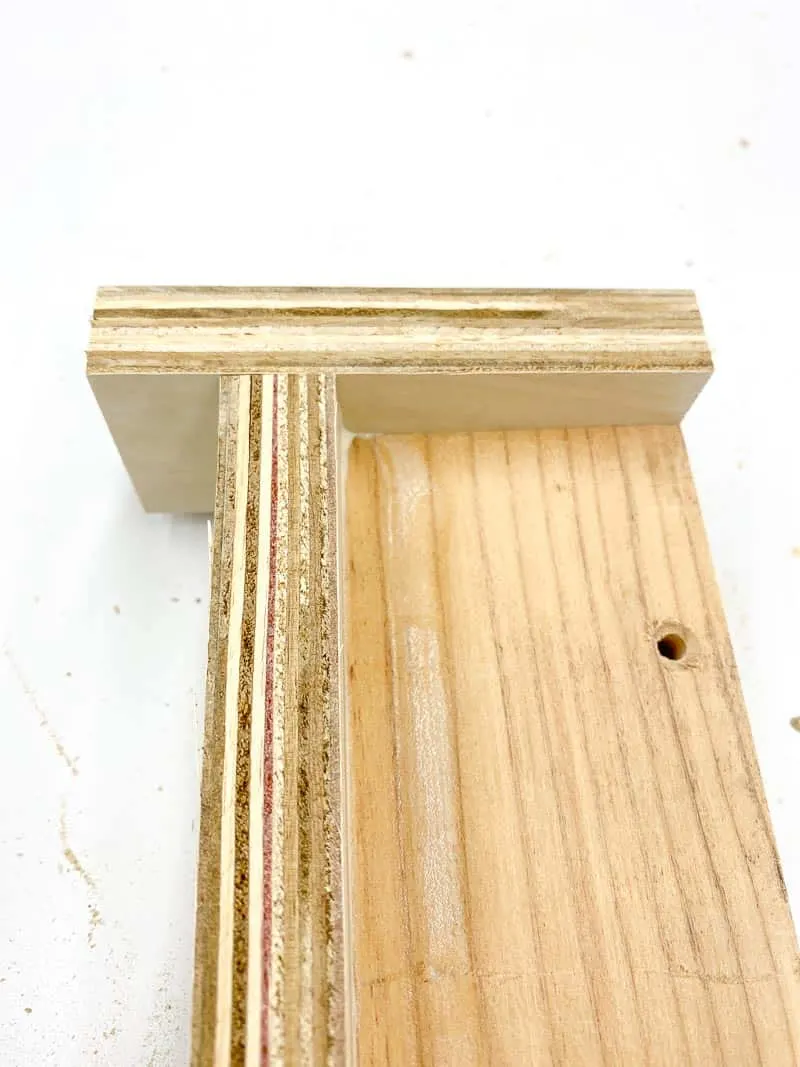
Attach the 2x4 side of the bracket to the sides of the table saw stand base (this also gives the saw a little more support to prevent the plywood from sagging over time). Then slide the tray into the bracket!
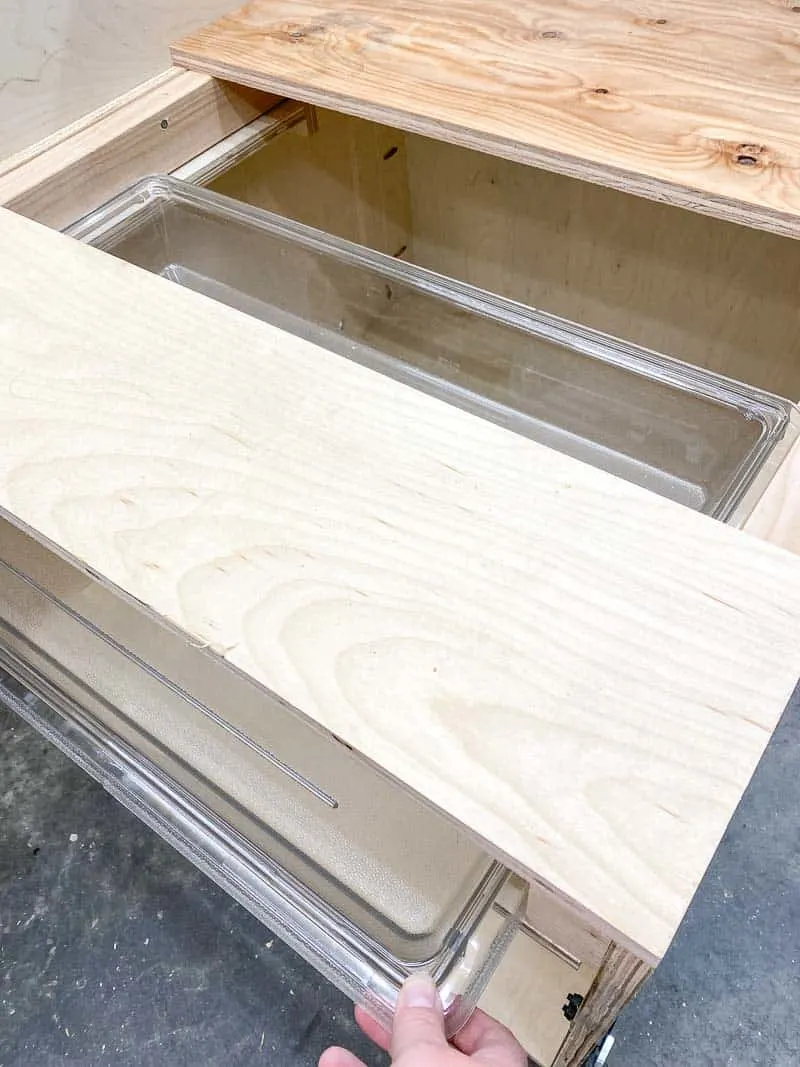
The shelf underneath is supported by two scraps of plywood nailed to the sides. I left it loose so I can slide the shelf out to clean it or retrieve anything that gets pushed too far back.
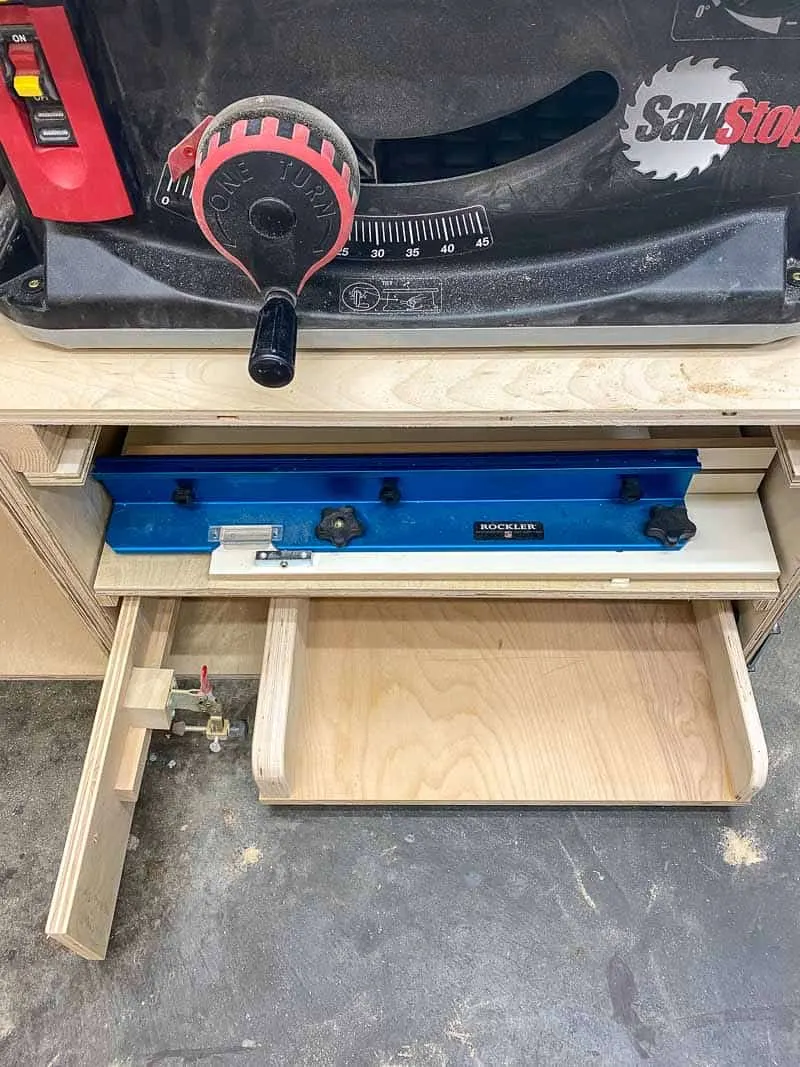
Add shelves and drawers
You can customize the drawers and shelves to fit your needs, so I won't get into the specifics too much. I have a full tutorial on how to build drawers three different ways here if you're interested in learning more.
I used a shelf pin jig to drill holes for adjustable shelves first.
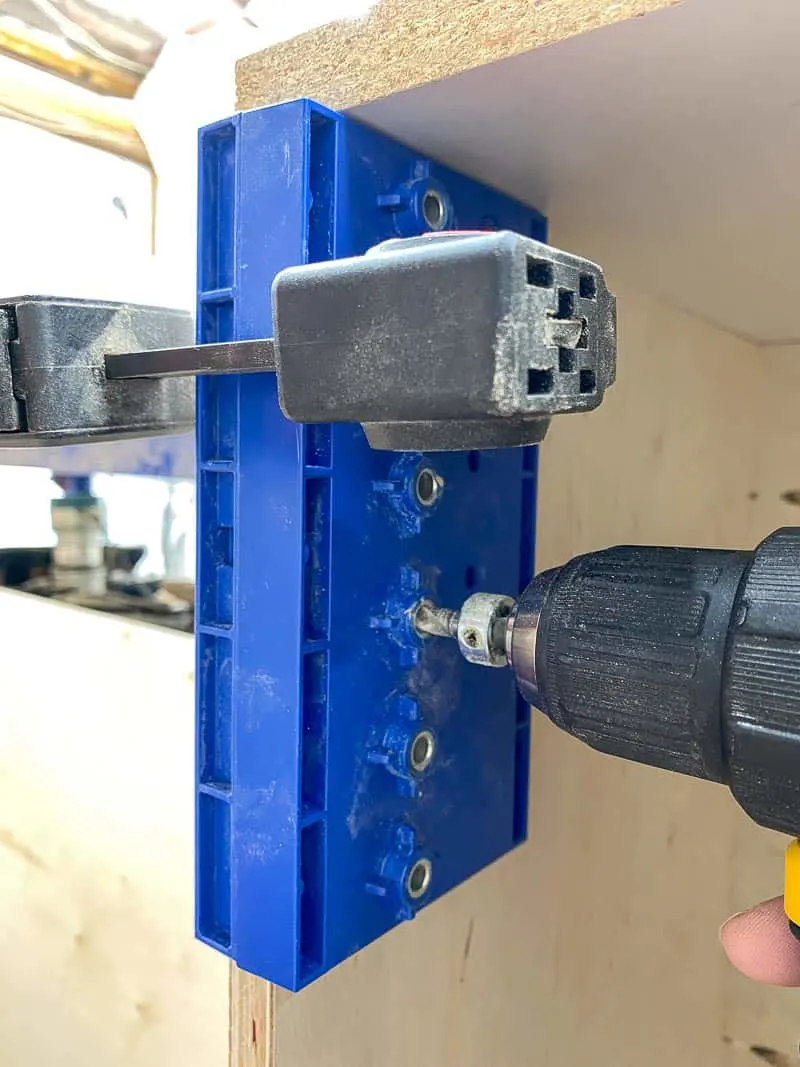
I had a leftover scrap of OSB from building my garage shelves that ended up being a perfect fit! These bins are great for keeping similar items together, like my dowel jig and dowels. The width is just right for Festool systainer boxes too!
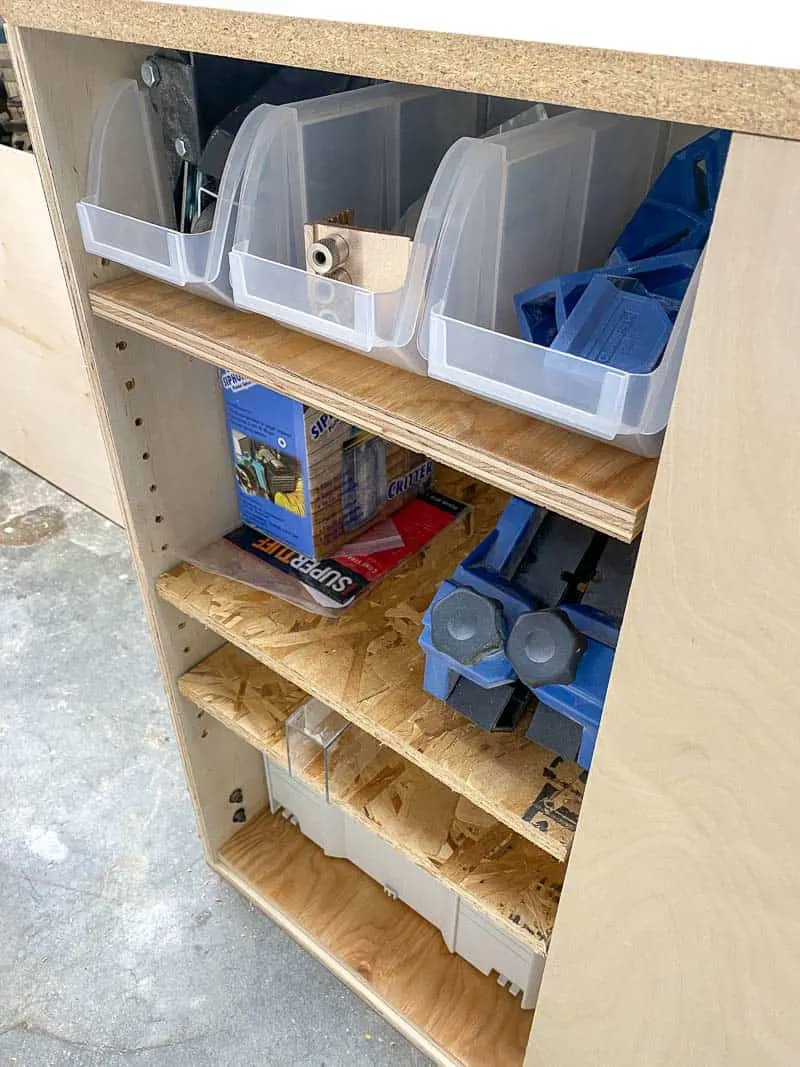
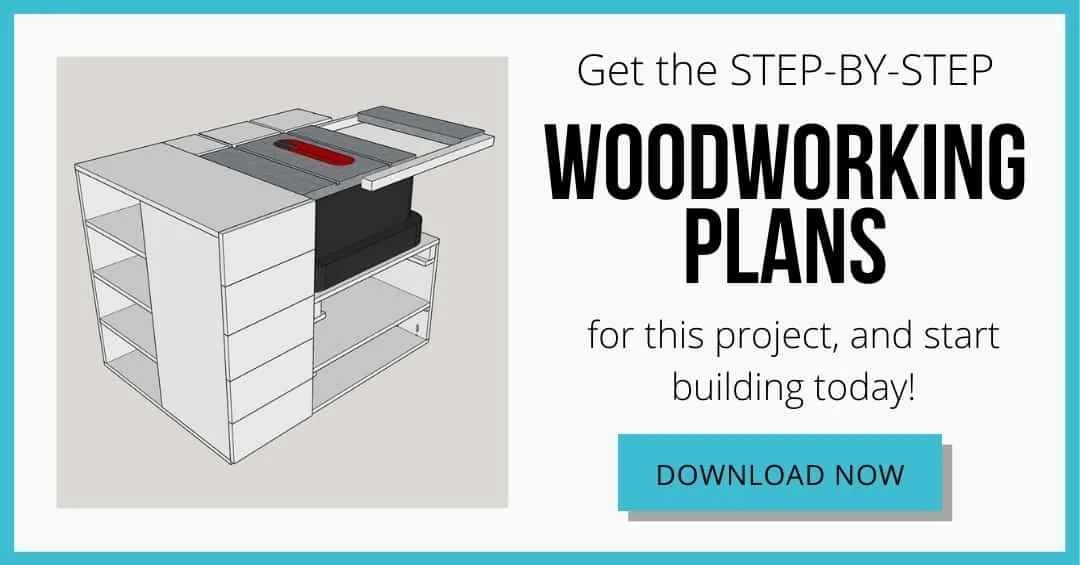
The drawers were made from all the narrow plywood cutoff pieces I keep in my lumber cart. Some are only three inches deep and some are six. Some are made with ½" plywood and others are ¾". It's shop furniture, and no one is going to notice but me! I just slapped drawer boxes together with wood glue and brad nails.
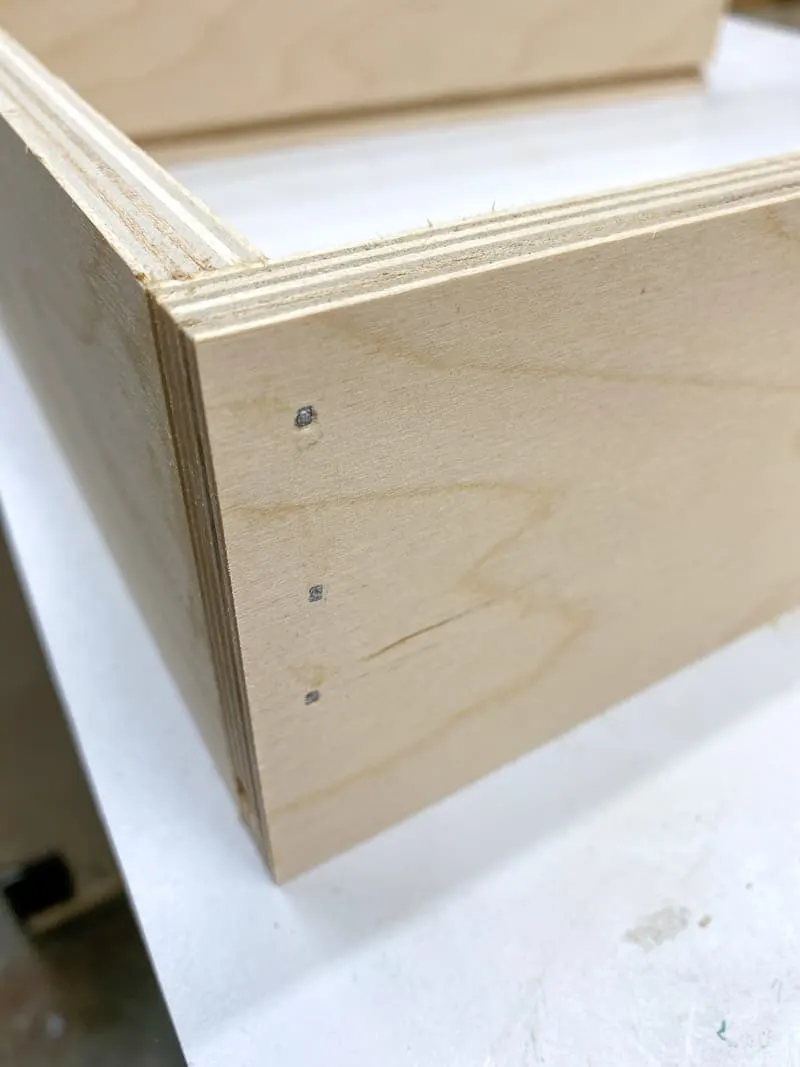
I kept all the drawer fronts the same height and width, so they overlay the front edge of the table saw stand. The drawer pulls are super low profile, so I don't injure myself when I inevitably bump into them while I'm busy working! They just hook onto the top edge of the drawer front and screw into place from the inside.
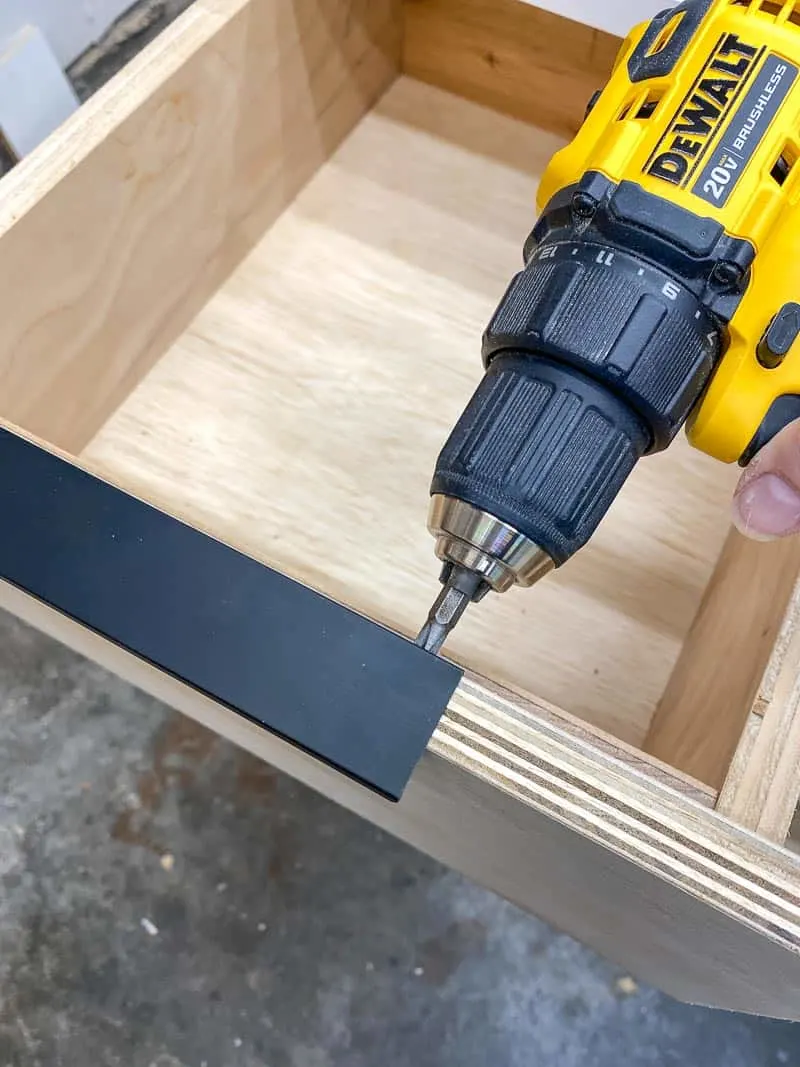
Enjoy your new table saw table!
My new table saw table has totally changed the functionality of my workshop! I can make safer, more accurate cuts with proper support, and I'm more likely to use my table saw for crosscuts instead of the miter saw.
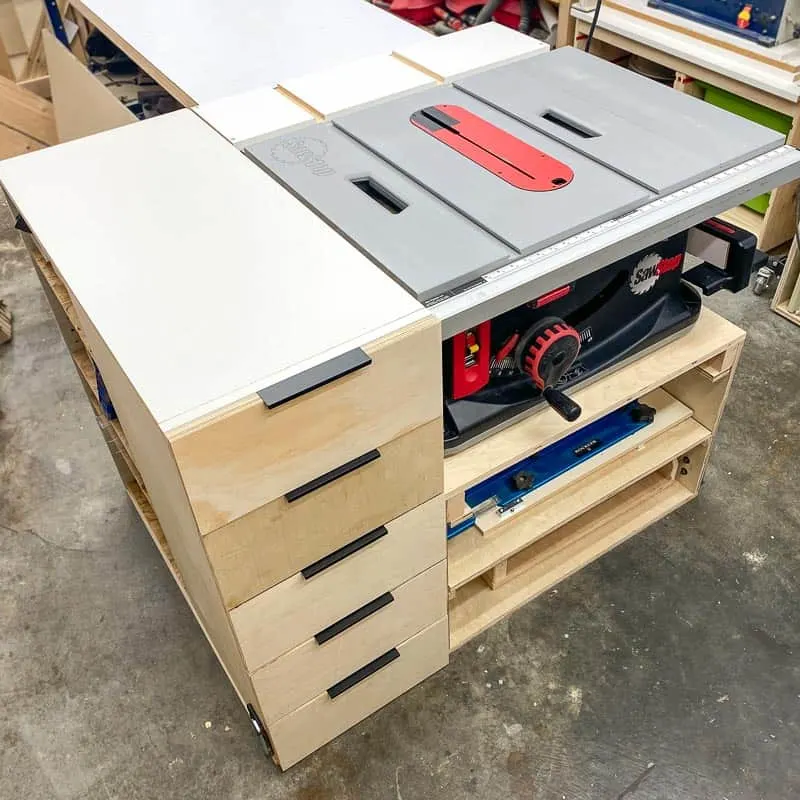
In a small workshop, every inch of space counts! I'm loving all the drawers and shelves for smaller items.
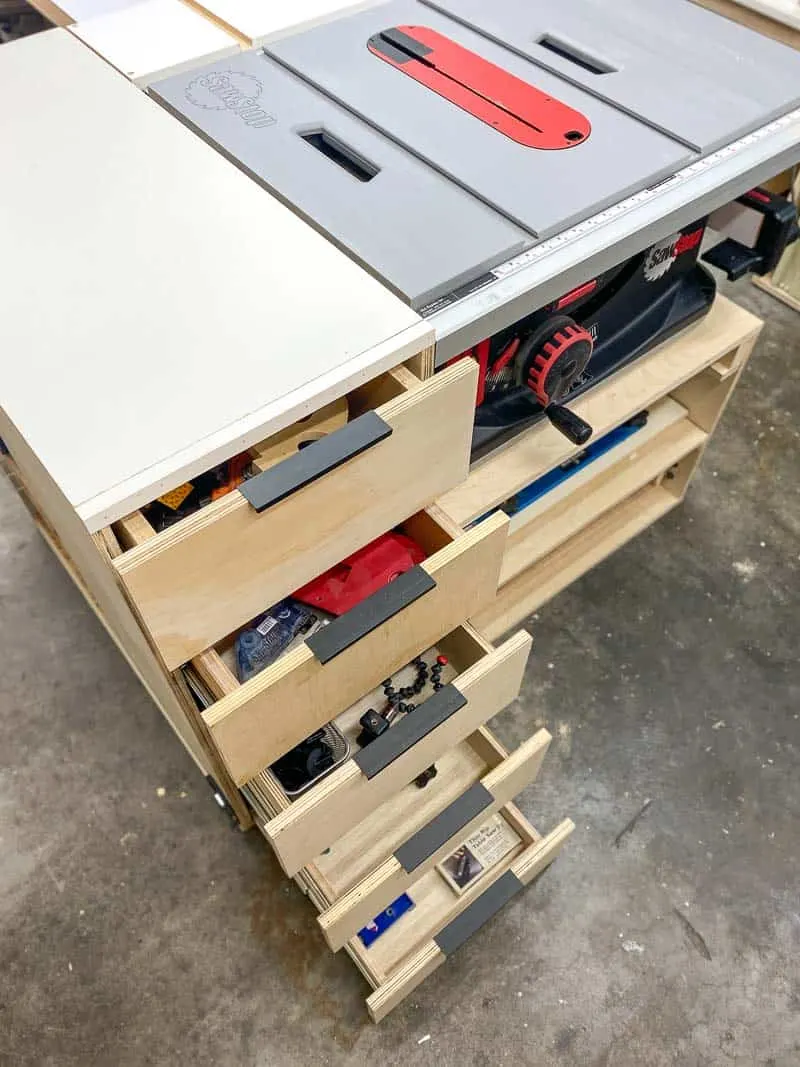
If I ever need to move the table saw stand, I can just slide the casters into these brackets and roll it away!
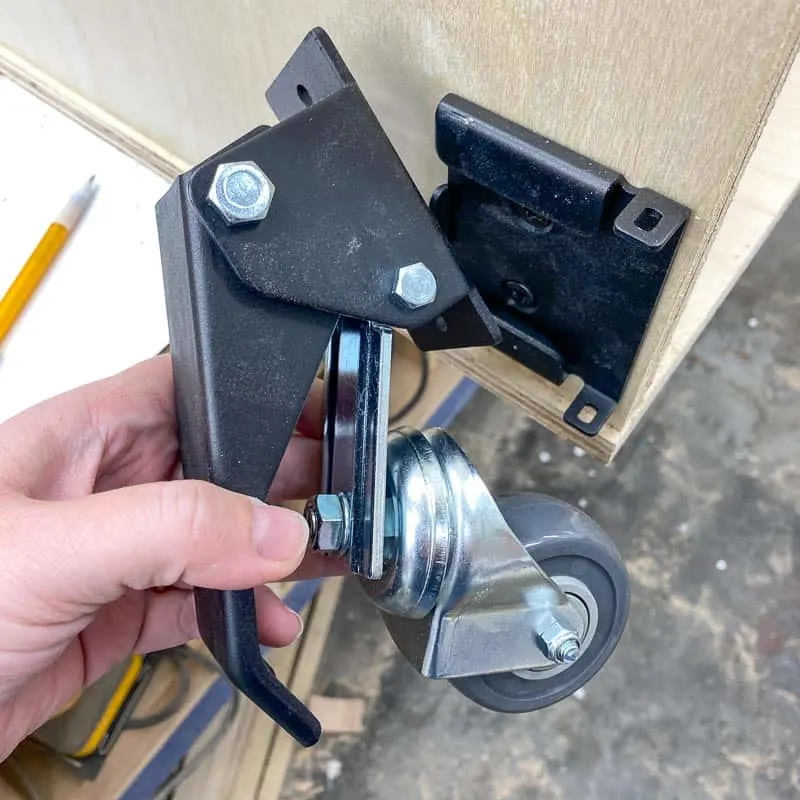
I can't wait to get started on my next build with this new set up! This is one of those projects that you'll wish you had made sooner. Download the plans with all the dimensions, a cut list and plywood cut diagram, and step by step instructions by clicking the box below!
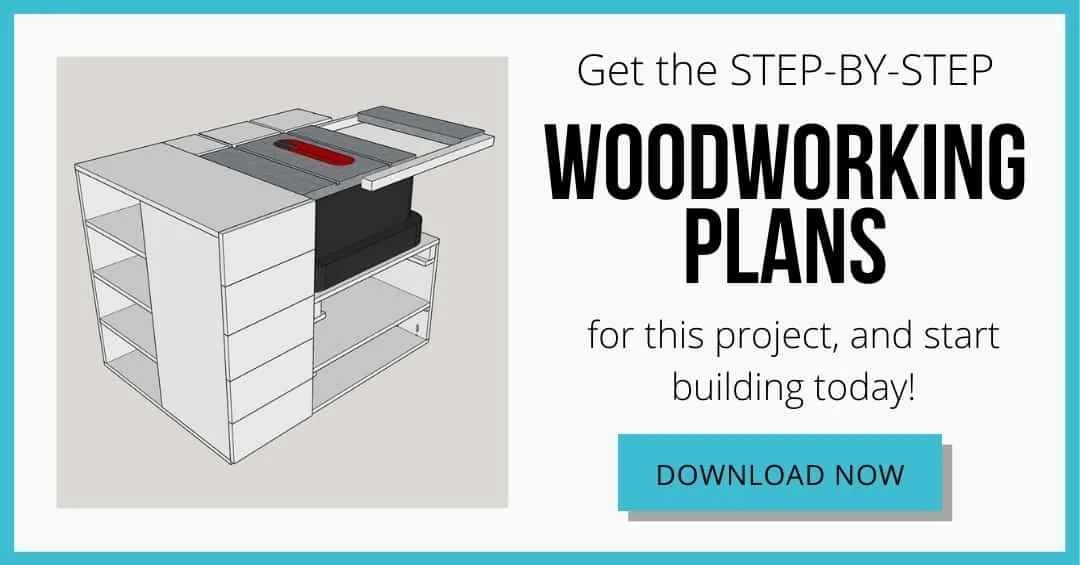
James Rawlings
Sunday 10th of January 2021
Veneta, I have your table saw plans and I have some questions. First, why are there 2 parts for the saw bottom (Parts D & E)? Next, why is the Top Back (Part M) 8 11/16" wide. Assuming that the Back (Part B) is 3/4", there will be a 1/16" gap along Part M. I suggest for future projects, you include an "exploded" view with parts labels. I use Sketchup to model all projects so that I can catch any project errors before I cut anything. An "exploded" view would be extremely helpful. To save space, I plan on eliminating the drawer cabinet on the left. The Top Left (Part U) will be foldable like on drop leaf table. Lastly, I love your plans!
Vineta
Monday 11th of January 2021
The table saw bottom has two parts to allow space between them for the sawdust to fall into the tray below. One piece is wider than the other to account for the dust collection hose behind the saw. You can certainly make the bottom out of one piece, but you'll end up with sawdust collecting underneath the saw that you'll have to suck up with a shop vac every once in a while.
For Piece M, you want a 1/16" gap between the saw and the top to allow the sliding fence to move freely. On the SawStop Jobsite saw, there are two bars on the front and back of the table that slide out to make wider cuts. I had to trim the top slightly to allow it to move. If you're using a different saw, your fence may work differently.
I love your drop leaf table idea for the left side! I'll also consider making an exploded view for more complicated builds like this one in the future. I use SketchUp to make my plans, so I should be able to do that pretty easily.
Barbara
Wednesday 30th of December 2020
I like the design. Am considering the build for my Dewalt jobsite saw, currently on scissor stand. However, I'm curious how easy it is to access the back of the saw. Once in awhile I have to make adjustments from the back of the saw to realign my blade to the miter slot. Also, I'm curious where the electrical cord comes out?
Vineta
Friday 1st of January 2021
The outfeed area behind the saw blade is attached with countersunk screws, so I can remove them and access the area behind the saw if necessary. There's 6-8 inches behind the saw, so it's not too difficult to reach in and make adjustments. The cord comes out through the same hole as the dust collection hose.
Greg
Saturday 5th of December 2020
Best table saw cart I have seen. done lots of research
Bucky
Sunday 18th of October 2020
Great write up! Just curious what kind of table saw do you have. Still not sure if I’m ready to add a table saw but a job site one seems like it may be a good route to go. Thanks!
Vineta
Tuesday 24th of November 2020
I have the SawStop Jobsite table saw. It's a great saw, and the safest one out there!